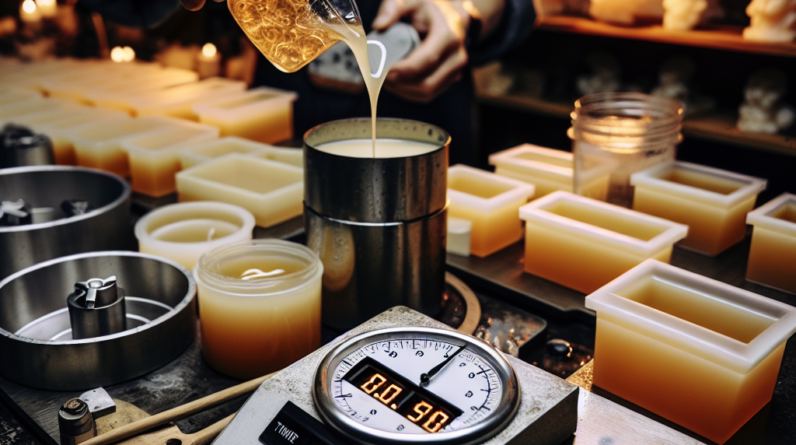
Understanding the Basics of Resin Candle Making
What is Resin Candle Making?
Resin candle making is a fantastic craft that combines beauty with creativity. As someone who has delved deep into this realm, I can first hand how rewarding it can be. The basic idea involves using epoxy resin instead of traditional wax as the primary material for your candles, which allows for cool designs and the potential for unique inclusions.
The process can be a bit daunting at first, but with proper timing and patience, you’ll find your rhythm. The part that’s usually the most nerve-wracking is getting the resin to set just right—too fast, and you’re left with imperfections; too slow, and it becomes a gooey mess.
As you get into the groove, it’s essential to focus not only on the materials but also on environmental factors like temperature and humidity. These elements can significantly impact how your resin behaves, so keep an eye on them!
Tools You’ll Need
Before jumping in, it’s crucial to have the right tools to smooth out the production process. Trust me, I’ve learned the hard way that skimping on this part is a no-go! You will need mixing cups, stirring sticks, a heat gun, and molds that suit your creative vision.
Don’t forget safety gear! Gloves, masks, and protective eyewear go a long way. I’ve had my fair share of resin splatters, and let me tell you, they’re not fun to clean up! Ensuring you have a dedicated workspace will help keep everything organized and to minimize mess.
Lastly, you may want to consider investing in a good scale, as precise measurements are key when mixing resin and hardener. Accurate timing is essential—it’s all about the right mix to get that perfect burn!
Choosing Your Resin
Now, let’s talk resin. There are several types available, and each one carries its own unique qualities. Some cure faster, while others take their time, which will affect your production schedule. I often lean towards the medium viscosity resins—they offer a nice balance of workability and cure speed.
Don’t forget to check if the resin is suitable for candle making; not all resins are created equal! I’ve made the mistake of grabbing the wrong type before, and the results were less than desirable.
Speaking of results, consider testing a small batch first. This will help you gauge how the resin behaves and what crafting adjustments you might need to make. There’s nothing worse than being excited about a new design only for it to flop on production day!
Perfect Timing in Mixing and Pouring
Measuring and Mixing
Getting the mix right is where timing becomes critical. I always mark my mixing cups with measurement lines to ensure consistency. It’s like, you wanna make sure each batch is perfect, right?
When mixing resin and hardener, make sure to follow the manufacturer’s recommended ratios. I can’t emphasize enough how important it is to take your time when mixing; it’s not just about speed but also about thoroughly incorporating the components.
Patience pays off! Mixing too fast can introduce bubbles that compromise the aesthetic of your candles. No one wants a bubbly finish. So, find your zen while mixing—slow and steady wins this race!
Pacing Your Pour
Once you’ve got that mixture down, it’s time for the pour. I’ve found that pouring at the right temperature helps avoid any weird crystallization issues later on. The ideal range tends to be around 70°F to 80°F; it allows for a smooth pour with no hiccups.
Think of this as an art form! Pour slowly and try to aim for the edges of your mold; it creates a more even distribution and prevents air bubbles from forming underneath. I’ve realized that pouring from a height can help with this, too.
But keep an eye on the clock! Some resins have a “working time” where they remain pourable before they begin to set. Getting impatient can lead to disaster. So, be sure to time your pours accurately!
Waiting for the Cure
Now, the hardest part of the process is waiting! Patience is key while the resin cures, which can take anywhere from several hours to a day, depending on the type of resin you use.
In this period, try to resist the urge to mess with your candles. I used to check them frequently, which only led to disruptions and longer cure times. Just trust the process and let them be. Keeping the workspace at a stable temperature can help the curing process immensely.
A little tip: while you wait, use that time to brainstorm your next batch! That way, when your candles are finished, you’re already ahead of the game.
Finishing Touches and Quality Control
Demolding with Care
Once the resin has fully cured, it’s time to demold. This is either the most exciting or the most nerve-wracking part. I tend to slyly wiggle the mold a bit before gently peeling it away from the candle. Remember, patience is again key here! Rushing can lead to cracks or imperfections.
Sometimes, if the resin is too tightly bound to the mold, a little heat from a heat gun can work wonders—but be careful not to overdo it. It’s like seducing the resin out of its mold, giving it a glorious exit.
Enjoy that moment of victory, but don’t get too attached! Evaluate your work and see where there is room for fine-tuning for your next round of candles.
Inspecting Your Candles
Now that the candles are out, check for imperfections. Look for bubbles or cracks and see what you can improve for the next batch. Believe me, I’ve had my fair share of “projects” that didn’t make the cut for sale simply because I didn’t pay enough attention during this portion of the process!
If you spot any bubbles, I’ve found that a heat gun can help remove them. Just while you’re at it, make sure you’re not holding it too close. We want candles, not gooey blobs of resin!
This is also the perfect time to consider any additional touches, whether it’s adding scents, color, or embellishing your candles with labels. These final improvements can set your work apart from the rest.
Testing the Burn
After everything, you gotta test the burn. Light up a candle and see how it performs. This is crucial! I’ve also tried to test a few burns before showcasing my work, as it gives me insight into things like wick size, burn time, and scent throw.
Keep a notepad handy during this part of the process. Noting down what works and what doesn’t can be a lifesaver for future creations.
Don’t forget to share your findings with friends or fellow candle makers. Feedback is a gift—we all want to improve, and collaborating often leads to those ‘aha!’ moments!