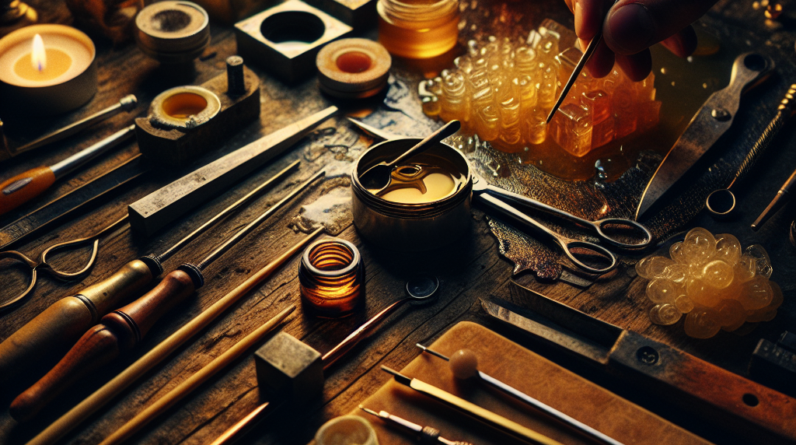
Hey there, fellow candle makers! If you’re here, you probably want to take your resin mixing game to the next level. I’ve been playing around with resin for a while now, and I’m excited to share some advanced techniques that will help you create stunning candles. Let’s dive in!
Understanding the Basics of Resin Mixing
What is Resin?
Resin is a fantastic material used in candle making due to its unique properties. It’s a type of liquid plastic that hardens when mixed with a hardener. This process creates a durable, glossy finish that looks amazing in candles. However, not all resins are created equal. Some are designed specifically for candle making, while others are better suited for other crafts.
Knowing your resin is super important because it affects how your candle turns out. You can create all sorts of cool effects and finishes, depending on the type of resin you use. My go-to is usually epoxy resin—it’s generally user-friendly and offers a glass-like finish that’s just stunning!
Before mixing, make sure you read the instructions on the label. Different resins have different mixing ratios, so getting that right is crucial for the final product. Trust me, you don’t want to end up with a sticky mess!
Choosing the Right Tools
Let’s talk tools! When mixing resin for candles, having the right utensils is key. I always have mixing cups, spatulas, and gloves on hand. It’s not just about making a pretty candle; it’s also about working safely and effectively.
A good set of mixing cups is essential, preferably ones that are graduated so you can measure accurately. I also use silicone spatulas, as they’re easy to clean, and I just love how they scrape every last drop of resin out of the cup!
Don’t forget about gloves! Resin can be a bit tricky and can irritate your skin, so it’s always a good idea to protect your hands. Plus, let’s be real—I just hate getting my hands all sticky when I can easily avoid it!
Temperature Considerations
Temperature plays a significant role in the mixing process. If it’s too cold, the resin will thicken, making it hard to work with. On the flip side, if it’s too hot, it might cure too quickly, leading to bubbles and imperfections.
I usually find that the ideal temperature for working with resin is between 70-80°F (21-27°C). If the temperature in your workspace doesn’t match this, don’t worry! You can warm your resin slightly, or move to a warmer area for mixing.
If you’re working in a cold environment, try using a heat gun or a hairdryer set on low. Just keep it at a distance! You don’t want to cook it; you just want to warm it up a tad. This little trick has saved me many a failed project!
Creating Stunning Colors and Swirls
Dyes vs. Pigments
Choosing the right coloring agent is super important for achieving the look you want. Dyes are great for achieving transparency and a more subtle color, while pigments give you that vibrant opaque finish. Depending on the look you’re aiming for, use one or the other—or even both!
When I first started, I experimented a lot with both, and my favorite has become the pigment powders. They add such depth and richness to the resin. Plus, you can mix them to create your own unique shades!
Always start with a small amount of colorant first, then mix it to see how it looks. You can build up the color gradually until you find the perfect balance. Honestly, it’s all about experimenting and having fun.
Mastering the Swirl Technique
The swirl technique is one of my favorite ways to add some flair to my candles. To do this, pour two different colors of resin into your mold, then use a stick or a spatula to gently swirl them together. Don’t overdo it, though! You want to see the dance of colors and not a muddy mix.
One tip is to pour the colors at the same height. This way, they layer nicely, and you don’t lose that beautiful contrast. I always find that less is more with swirls; you can always add more if you want a bolder look.
After swirling, let it sit for a moment before you start adding in any embellishments, like glitter or flowers. This helps keep the swirl intact and ensures they don’t sink to the bottom. It’s all about timing!
Embedding Objects
If you want to take your candles to the next level, try embedding objects in your resin. Whether it’s dried flowers, shells, or even little charms, they add a personal touch and make your candles unique. Make sure that whatever you’re embedding is dry and clean to prevent any unwanted reactions.
I usually start by pouring a thin layer of resin into the mold first. After that, I arrange my objects and then pour more resin on top. This way, you avoid them floating to the top, and they’re nicely encased within the resin.
Don’t be afraid to get creative with this! I’ve seen some stunning designs, from nature-themed candles to funky, colorful pieces with retro toys inside. It’s all about letting your personality shine through!
Finishing Touches and Curing
Demolding Your Candles
Once your candles have cured, it’s time to pop them out of the mold! But hang on a second—patience is key. I usually let my candles sit for at least 24 hours before demolding to ensure they are fully cured and set. Rushing this step often leads to cracks or other damage.
When you’re ready, gently flex the mold to loosen the edges, then carefully pull the candle out. I like to support the base with one hand while gently tugging on the sides. If it’s stubborn, give it a little wiggle! But seriously, no need to pull; we’re not trying to wrestle here!
Once out of the mold, you might have some rough edges. A quick sand with fine-grit sandpaper can smooth them out. Just ensure you don’t overdo it; we’re aiming for a polished product, not a completely different shape!
Adding Finishing Touches
Now the fun part—adding your finishing touches! I love to personalize my candles with labels, ribbons, or even little charms. It’s all about that presentation, and it can really elevate your finished product to the next level.
When applying labels, make sure you use waterproof labels. Resin can be a bit messy, and you don’t want your labels peeling off. I’ve learned this the hard way, trust me!
Lastly, think about how you want to package your candles if you’re gifting them or selling them. A cute box or wrapping goes a long way in making your candles feel really special. Remember, you’re creating a product that people will love!
Curing Process Tips
The curing process is crucial for a beautifully finished candle. While you might be tempted to touch it, resist the urge! The resin needs time to harden and develop its structural integrity. Generally, I recommend curing times between 24 to 72 hours, depending on your resin brand.
During the curing process, make sure to keep your candles in a dust-free environment. I often place them in a box to prevent dust and debris from sticking to the surface. Trust me—this is a game changer for that glossy finish!
After curing, have a look at your finished product. You might notice small air bubbles. If they are a bother, don’t fret! A little bit of fine sanding can take care of that, and you can also apply a clear coat of resin for that extra shine!
FAQs
1. Can I use any type of resin for candle making?
Not all resins are suitable for candles. Look for epoxy resin or specifically labeled candle-making resin. They’re designed to handle heat better and avoid release of harmful fumes.
2. How can I avoid bubbles in my resin?
Bubbles can be a pesky issue! Mix slowly, avoid stirring too vigorously, and you can also use a heat gun or torch to pop them. A little patience goes a long way.
3. What can I add to my resin candles for some unique looks?
You can add dried flowers, glitter, shells, or little trinkets. Anything that’s dry and clean can generally be embedded, so get creative!
4. How long should I let my candles cure?
Curing times can vary, but I recommend letting them sit for 24 to 72 hours, depending on the resin instructions. Always follow the manufacturer’s guide for the best results.
5. What’s the best way to clean resin tools?
Cleaning resin tools can be a pain, but it’s totally doable! Use rubbing alcohol or a dedicated resin cleaner while the resin is still wet. For dried resin, you might need to soak them a bit to get them clean.