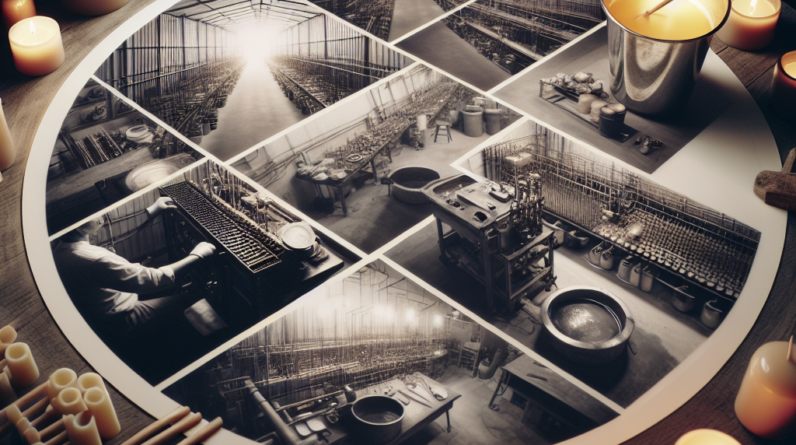
Material Collection and Preparation
Choosing Quality Materials
When I first dove into the world of resin candle making, I quickly learned that the materials I chose set the foundation for the entire project. High-quality resin, wicks, molds, and fragrance oils are crucial if you want to end up with a stunning finished product. Each component plays a vital role in ensuring your candles burn properly and look fabulous.
Not only do you want to consider the quality, but you’ll also want to think about the aesthetics. Choose colors and scents that resonate with you and your audience. It’s all about striking that perfect balance between beauty and functionality. Trust me, your candles will stand out way more with thoughtful material choices!
Lastly, don’t shy away from exploring different suppliers. Sometimes, the best materials come from unexpected places. Experimenting with various brands can lead to discovering unique textures and finishes that will make your candles one-of-a-kind. So, stay curious and keep experimenting!
Prepping Your Workspace
Creating candles can get a little messy, so setting up an organized workspace is essential. I remember my first attempt where I ended up with resin everywhere—thankfully, it comes off, but what a hassle! I recommend covering your surfaces with drop cloths or newspapers to catch any drips.
Make sure you have all your tools handy—mixing sticks, measuring cups, and a thermometer should be within arm’s reach. I usually designate a specific area just for candle-making. Once everything is organized, it makes for a much smoother process and less cleanup later.
This organization leads to a better flow when you’re in the zone, mixing and pouring that resin. The less you have to hunt for supplies, the more you can focus on crafting beautiful candles that light up someone’s day!
Safety First!
As much fun as making resin candles is, we can’t forget about safety. Those strong-smelling resins can be harmful if inhaled, so I always recommend working in a well-ventilated area. Open a window or, even better, work outside when possible!
Protective gear is also a must. I wouldn’t dream of working without gloves and goggles—just a tiny splash of resin can ruin your day! When dealing with heat, be cautious with your pouring tools to avoid any burns or spills.
Knowing the safety protocols makes the experience much less intimidating and way more enjoyable. So, gear up and let’s get crafting safely!
Resin Mixing Techniques
Understanding Resin Components
Getting to know the different components of your resin is key. The resin itself typically comes in two parts: the resin and the hardener. Mixing these at the right ratios is the magic sauce that makes everything work. If you mess this up, it can lead to sticky candles, which is definitely not the vibe we’re going for!
Every brand has its own guidelines for mixing, so make sure you’re reading the instructions carefully. Explain it like a recipe—follow it closely to get the best results. I’ve learned the hard way that eyeballing it just doesn’t cut it!
Additionally, patience is your best friend here. Allowing the resin to warm up before mixing can enhance the blending process and lead to fewer bubbles. It might take a bit longer, but trust me, your end product will shine that much brighter.
Mixing for Color and Texture
One of the coolest parts of candle making is adding color! When I first started, I was all about the vibrant hues, but I quickly learned that less can be more. Start with small amounts of dye and gradually increase; you can always add more but can’t take it back once it’s too dark!
Texture is another playful way to elevate your designs. Try incorporating sand, herbs, or glitter to give your candles a unique twist. Each element can add a story, a vibe, or even an aroma reminiscent of the beach, a garden, or a cozy campfire.
Keep in mind that the color might change slightly as the resin cures, so always test your colors to find out how they transform once dried. Sometimes it’s a pleasant surprise, and other times… well, let’s just say I’ve had my fair share of oopsies!
Mixing Techniques that Work
Make sure to utilize a slow mixing technique to minimize air bubbles when combining the resin and hardener. I used to go in there with a wild swirl, but that just resulted in bubbles that popped up like popcorn! A slow and steady approach makes a big difference.
Another tip? Use a heat gun or torch to eliminate those pesky bubbles once poured into the mold. Just a quick pass over the surface works wonders, leaving you with a clear finish. Just be cautious—too much heat can warp your mold or mess with the curing process!
Lastly, always check varying temperature conditions of your workspace. If it’s too cold, you can face a longer curing time. Be prepared by keeping your materials at room temperature before mixing to achieve optimal results!
Candle Molding Fundamentals
Choosing the Right Mold
Picking the right mold really sets the tone for your candles. Whether you opt for traditional cylindrical molds or something out-of-the-box, your choice will affect both the look and the burn time. I remember going for a novelty shape mold once; it looked great but was a total pain to get out!
Consider the size of the mold, too. If you make larger candles, they tend to burn longer, while smaller ones are great for quick and easy gifts! Make sure to align your mold choice with your target audience or occasion.
Finally, don’t overlook the importance of mold release. Using a spray or alternative release agent can save you a lot of heartache during the demold process. Trust me; it’s not fun when your masterpiece gets stuck!
Pouring Techniques
When it comes to pouring, a steady hand makes a world of difference. I used to pour too quickly, which would result in spills and unevenness. Start by pouring from the edge to minimize splashing and ensure that the resin flows smoothly into the mold.
The temperature of your resin before pouring plays a part too. I’ve learned that just the right warmth ensures a more fluid pour and helps prevent air bubbles from forming. Check your materials’ instructions for the ideal range.
And, of course, be patient! Allow each layer to set if you’re creating multi-layered candles. This gives each layer a chance to bond properly and prevents any unintended mess-ups. It may take extra time, but it’s so worth it for the final look!
Dismolding Your Candles
Once your candles have cured, dismolding is the moment of truth. I used to dread this part, thinking I’d ruin my creation. Gently flex the mold to loosen the edges, then turn it upside down and give it a light tap. Patience is essential here—rushing can lead to cracks.
If you find it’s still stuck, placing the mold in the freezer for a few moments can help. The temperature change makes it easier to pop out those candles without any damage. I’ve learned this trick the hard way, and it works like a charm!
Always check your candles for any imperfections after dismolding. Small touch-ups can be done with a heat gun if you spot any bumps. It’s all part of perfecting your artistry!
Add Finishing Touches
Scent Selection
Oh, adding scent is where the magic really happens! Choosing the right fragrance can evoke emotions and memories, making your candles more than just decor — they become experiences. I absolutely love using essential oils combined with fragrance oils to create a unique blend.
When adding scent to your candles, always look for the recommended fragrance load for your resin, or you may end up with a scent that’s too weak or overwhelming. I’ve been there, and it’s a bummer when your candles don’t smell as good as you imagined!
Experimentation is key—mixing different scents can lead to delightful surprises. Just make sure to keep notes on your formulas for future batches. You’ll want to replicate those marvelous scents when you impress your friends!
Packaging & Presentation
Once you’ve got those beautiful candles ready, it’s time to think about how to present them. The packaging can often make or break the customer experience. I always love putting time into creating elegant designs that reflect the vibe of the candle inside.
Consider using eco-friendly packaging materials if you’re promoting a sustainable brand. It resonates well with customers who care about the environment, and it also shows that you value the planet too—win-win!
And don’t forget about labeling! A beautiful label with a great description can help convey your candle’s story. Think of it as an extension of the candle itself; it should be just as appealing and invite curiosity!
Final Quality Check
Before you hit “send” or “shelf,” always do a final quality check. I can’t stress this enough! Examine your candles for any imperfections, ensure they burn correctly, and check the scent throw. A little time invested here can save you from unhappy customers down the road.
Testing burn times is crucial; you want to provide accurate information to your customers. Document your findings so you can improve your processes for the next batch. Consistency is key to building trust with your audience!
Lastly, always ask for feedback once your candles are out in the world. It’s the best way to improve and learn what your customers love the most. Growing from their experiences will not only enhance your product but create an incredible sense of community!
Frequently Asked Questions
1. What materials do I need to start making resin candles?
You’ll need resin, hardener, wicks, molds, fragrance oils, and colorants. Don’t forget safety gear, like gloves and goggles!
2. How do I prevent bubbles when mixing resin?
Mix slowly and avoid whipping the resin. You can also use a heat gun after pouring to eliminate bubbles.
3. Can I use essential oils in my resin candles?
Yes! Just make sure to check the recommended fragrance load for your resin to avoid overpowering the scent.
4. What’s the best way to remove candles from the mold?
Gently flex the mold, tap it, or place it in the freezer if you encounter resistance. Patience is key!
5. How can I improve my candle packaging?
Invest time into thoughtful designs that reflect your brand. Eco-friendly materials and attractive labels can greatly enhance presentation!